NANJOのものづくり
創造の追求とものづくりへのこだわり
その先を見据えて
NANJOのものづくりは、メーカーでデザインされたものを製品化するだけではなく、時代の流れの中で常に先を見続け、メーカーとともに新たな付加価値を持つものを創り出していくことです。
1970年代後半、自動車の内装はデザインを重視した形状に大きく進み始めようとしていました。
この潮流をいち早く捉えたNANJOは、真空成型機を用いた立体のドアトリムの制作を始めました。
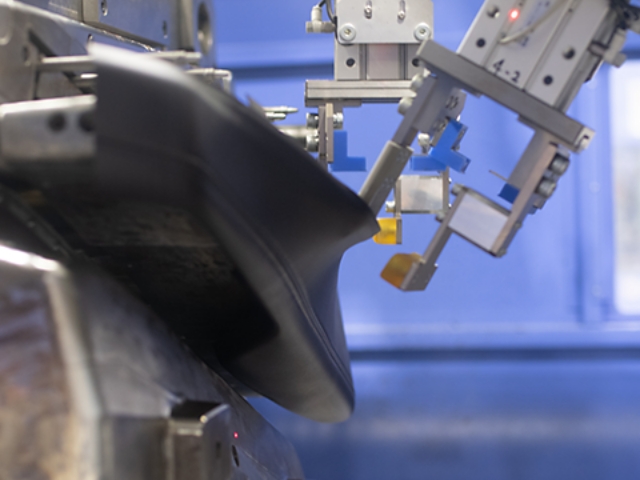
しかし、当時のNANJOには、汎用性の高い一般的な真空成型機しかなかったため、本格的な量産体制を考えると十分とはいえませんでした。より自動車の内装に適応した専用の真空成型機の開発には、課題がありました。
真空成型機は短期間で使い捨てるものではなく、10年20年と使い続けるものです。
その発注にあたっては、10年後20年後に、どのような自動車内装が求められるかを考えた上で真空成型機を発注しなければいけませんでした。
特に材質とサイズの将来予想は、進化し続ける自動車デザインを前提に考えると、極めて難しい問題でした。
NANJOのものづくりは、自動車の未来を見据えることであり、時代そのものを見据える作業と言えるでしょう。
クラフトマンシップ
新しい技術や新しい表現を生み出し可能性を広げ品質の向上を図っていく。それには、多くの時間と労力が必要になります。しかし、それが未来に向かって価値あるものを生み出すならば、これから先も創造の追求とものづくりへのこだわりをNANJOのクラフトマンシップとして大切にしていきます。
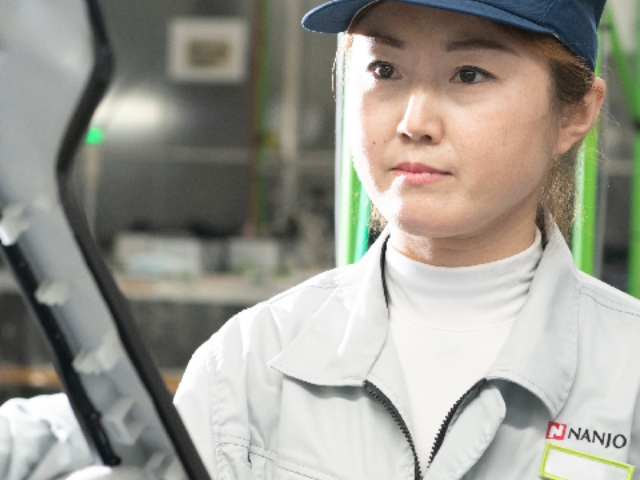
自らに責任を持つ
あらゆる要素を考え抜いて発注した機械が、必ずしも思ったように稼働してくれるとは限りません。
機械の不具合や現場に合わない場合でも、メーカー任せではなく、自分たちで対処しようとするのがNANJO流。
工場に並ぶ製造機械は、発注時にメーカーと一緒に開発するが、基本的には汎用機をベースとしています。
ものづくりの現場で完璧にフィットしないこともあります。
だが、NANJOの製品はオーダーに対して100%応えるものでなければいけない。
その100%を知っているのはNANJO自身。
だからこそ、100%の達成に向けて自身で製造機械を改善していきます。
使う道具や機械、設備を、自らより良く使いやすくしていこうという考え方は、NANJOが創業以来受け継いできた風土でもあります。
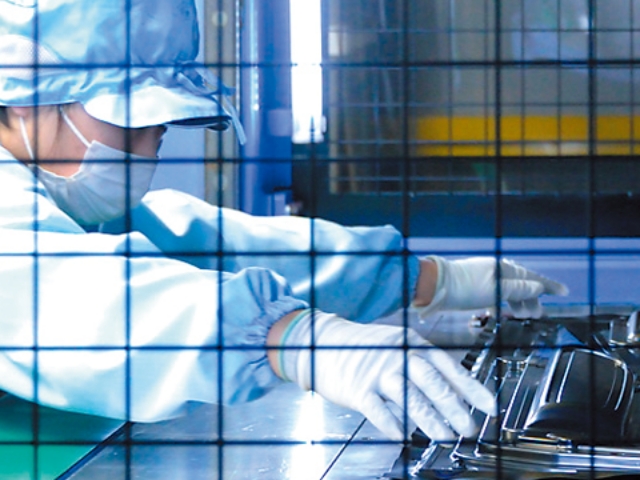
未来への進化と過去との融合
1990年、三次元形状の樹脂化を大きく進めることとなったNPM(Nanjo Press Mold)が導入されました。
それまでは、ウッドチップ基材を用いたドアトリムが主流でした。
そのドアトリムを樹脂ベースとすることで、ウッドチップ基材の歩留まりの悪さ、取り扱いの手間、環境課題への対応などの問題を解決するとともに、独自の集中管理機能もNPMに併せ持たせました。
その効果は大きく、表皮同時貼合や表皮部分貼合、樹脂むき出し製品の製造なども可能となり、NANJOの基幹工法として定着していきました。
しかし、その有用性に満足することなく、さらにその可能性拡大を図っています。
NPMの導入から約20年。さらなる質感向上を求め、1980年代後半に一旦現役を退いた凹引き真空成形技術を再び活用し、NPMと融合することで製品品質の飛躍的な向上を実現しました。
新しさを求めるだけでなく、持てる物すべてを投入し、より高い完成度を目指す。それがNANJOのものづくりです。
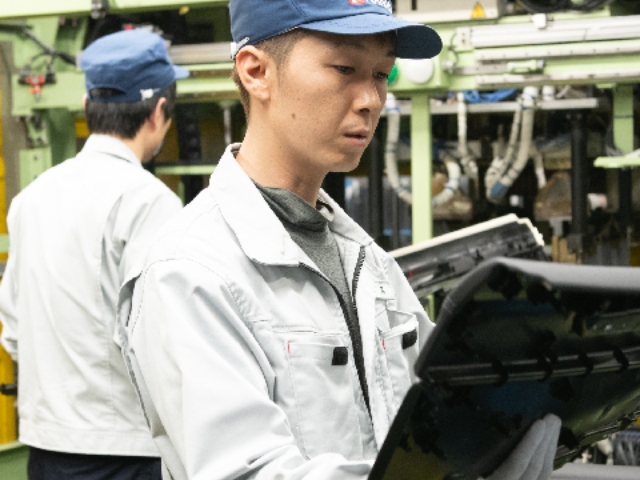
縫製の技術革新
時代の要求に応え、進化させる縫製技術。
NANJOの縫製技術はさらなる進化を遂げ、この10年で新しい段階に入りました。
従来の平面的な縫合を中心としたシート表皮の縫製に対して、立体物であるトリムパーツの縫製は、100年にわたって縫製技術を積み重ねてきたNANJOにとっても新しいチャレンジでした。
縫製オペレーターとして、新しい技術の習得はもちろん、それ以前に、従来とは異なる立体縫製用のミシンが必要となりました。
自動車の空間をより快適に、乗りたい空間へと演出するドアトリムは、スムースな面と、微妙に変化していく曲面で構成されたデザインを重視した形状に進化しています。
自動車メーカーやユーザーの要望に応えるために、ミシンメーカーとさまざまな面から検討や試作を続け、長年の試行錯誤の結果、NANJOのオリジナルミシンを開発しました。(本文の一部抜粋)
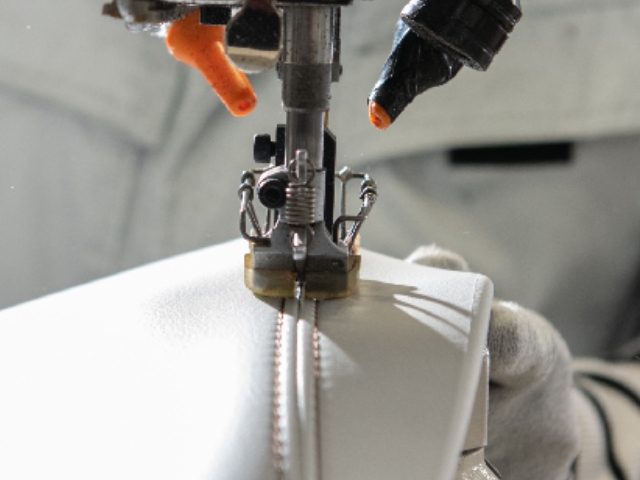